What is the 6S Method? A Guide to Building a 6S Lean Process
The 6S lean process is an enhanced version of the 5S system, integrating Safety into the standard five steps. It's a highly effective management approach in production and operations, especially in the context of Industry 4.0. The goal of the 6S method is to maintain a clean, organized, and streamlined workplace, which in turn optimizes efficiency and ensures workplace safety.
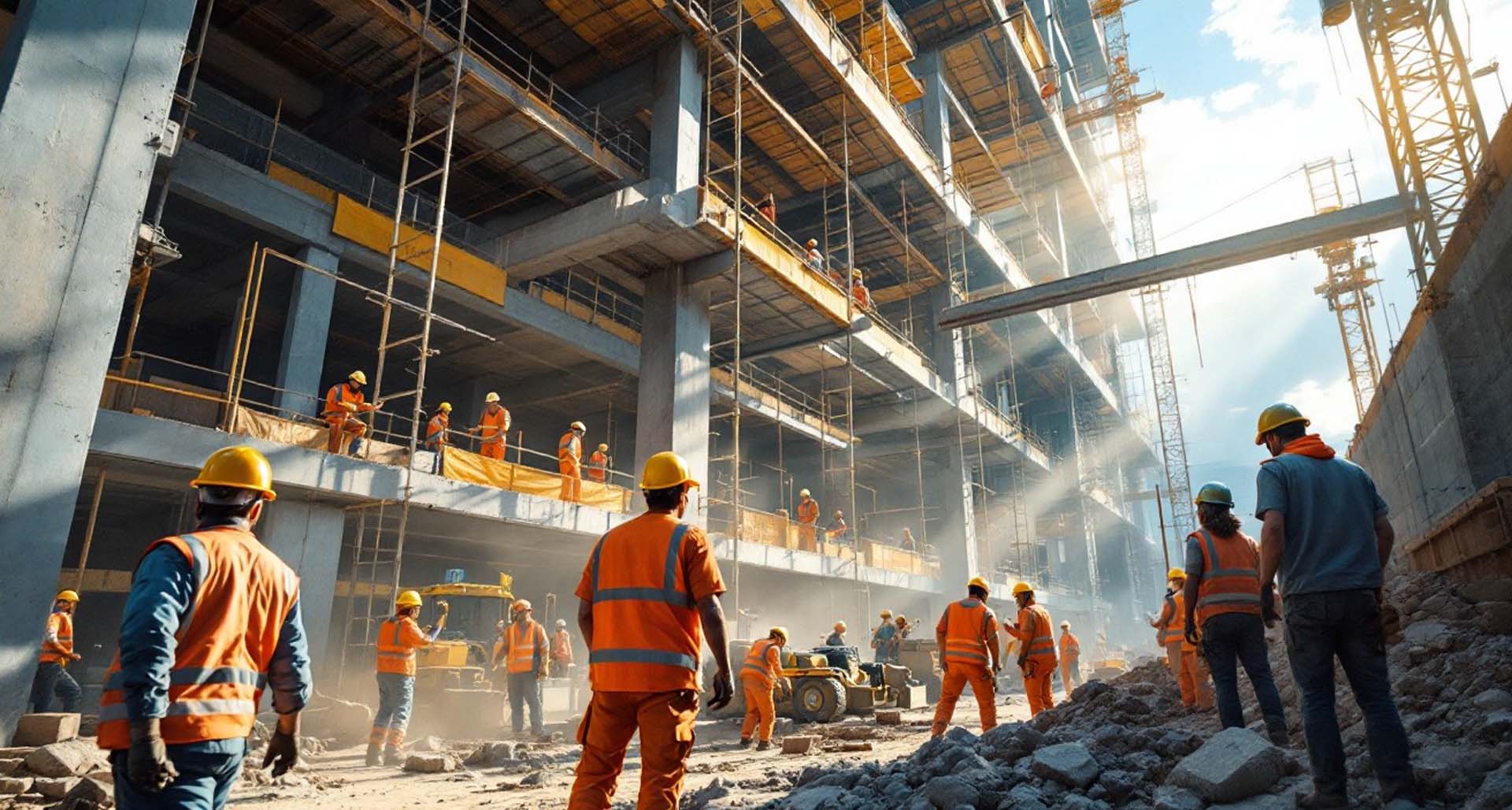
What is 6S Lean?
6S Lean is a development of the 5S principles, with the addition of "Safety," making it a more comprehensive approach to workplace management. It focuses on creating a safe, organized, and efficient environment by addressing not only the optimization of workplace processes but also the minimization of risks and hazards.
The Safety aspect in 6S Lean helps to maintain organizational continuity by reducing workplace accidents, improving occupational health, saving costs, and optimizing production time.
What Does 6S Include?
The 6S model consists of the following six key components:
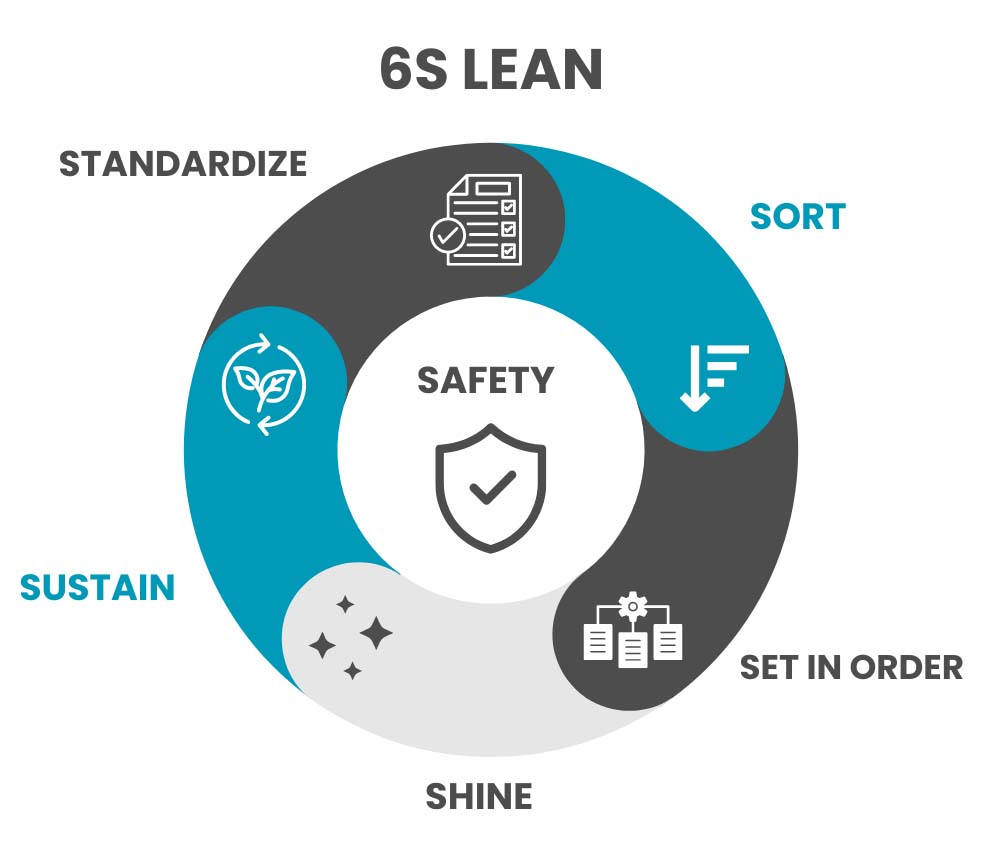
1.Sort (Seiri)
The first step in 6S focuses on sorting out unnecessary items from the workplace. The goal is to eliminate clutter, making it easier to identify essential items. The process includes "red tagging" items that are no longer needed, while "yellow tagging" can be used for items that may be useful in the future but are not immediately necessary.
2.Set in Order (Seiton)
In this step, items, tools, and materials are organized and clearly labeled to ensure they are easy to locate. The focus is on creating an organized workspace where everything has its place, making it easier to store and retrieve materials quickly.
3. Shine (Seiso)
The "Shine" step involves regular cleaning and maintenance of the workspace, equipment, and tools. It’s not just about cleaning for appearance but also about identifying potential problems like leaks or wear and tear. This process helps maintain a safe environment, reduces risks of slips and falls, and ensures cleanliness in production areas.
4. Standardize (Seiketsu)
"Standardizing" involves creating clear guidelines and processes that ensure the first three steps—sort, set in order, and shine—are consistently followed. It’s about creating routines, setting visual standards, and ensuring workers understand and adhere to best practices for organization and cleanliness.
5. Sustain (Shitsuke)
"Sustain" is about maintaining discipline and ensuring the 6S principles are consistently followed. This step often presents the greatest challenge because it requires continuous reinforcement and habit formation among workers. Regular audits, reviews, and encouragement from management are necessary to ensure ongoing compliance.
6. Safety
The last step, Safety, is crucial in the 6S model. This element was added to enhance worker safety and ensure that workplace hazards are minimized. Identifying potential safety risks and implementing preventive measures, such as safety training and emergency response procedures, are key components of this step.
The Role of Safety in the 6S Method
Workplace safety is paramount in any manufacturing environment, and 6S emphasizes this by addressing safety concerns at every step. A safe and clean work environment leads to:
- Increased productivity and quality of work
- Happier and more confident employees who feel safe
- Reduced accidents and injuries, leading to fewer disruptions and lower costs
At GAK, we believe that safety is the cornerstone of any modern manufacturing model, especially in Industry 4.0. A focus on safety helps reduce productivity loss from injuries, saving operational costs and promoting long-term worker health.
How to Implement 6S Lean Effectively in Your Workplace
To successfully implement the 6S lean method, you need to prepare several critical elements:
- Understand or Have Experience with 5S
The 5S principles form the foundation of 6S, so it’s essential to have a solid understanding of them (Sort, Set in Order, Shine, Standardize, and Sustain) before introducing Safety. - Identify and Report Risks
Implement a clear process for identifying and reporting hazards in the workplace. This ensures that safety risks are promptly addressed. - Safety Awareness Training
Provide training to employees on safety protocols specific to your industry. This will help them identify potential hazards and know how to respond to them. - Engage Employees in Discussions
Hold meetings and discussions with employees to share the 6S method. Encourage active participation and feedback to improve the process. - Get Management Support
Ensure that leadership supports the 6S implementation and provides the necessary resources and guidance for success.
Benefits of 6S Lean in Manufacturing
- Enhanced Productivity and Efficiency: With organized workspaces and clear guidelines, employees can find materials and tools quickly, reducing downtime and improving production flow.
- Improved Worker Safety: By identifying and mitigating risks, the 6S method significantly reduces workplace accidents, contributing to a safer and healthier environment.
- Reduced Costs: Fewer accidents, less waste, and better utilization of resources all contribute to significant cost savings for the company.
Higher Employee Engagement: Workers who feel safe and are part of a well-organized workplace tend to be more motivated and productive.
see more:
Conclusion
The 6S method is a powerful tool for optimizing workplace efficiency and safety in manufacturing environments. By integrating safety into the standard 5S approach, businesses can create a more streamlined, organized, and safe work environment that reduces waste, prevents accidents, and improves employee morale.
At GAK, we strongly advocate for the 6S approach to drive productivity and safety. Don’t forget to check out our protective clothing and reflective safety apparel to ensure your employees are working in the safest possible conditions.